6+ Equipment Damage Report Examples to Download
An Equipment Damage Report is an essential document used to record any damage that occurs to machinery or equipment within a workplace. The purpose of creating such a report is to track the specifics of what happened, determine how it happened, and suggest measures to prevent future occurrences. This report is crucial not only for maintaining the equipment but also for ensuring operational safety and efficiency. Incorporating elements of a Job Safety Analysis, it helps identify potential hazards that could harm workers and disrupt daily operations. By analyzing equipment damage in this structured way, companies can improve their maintenance routines and safety protocols, making the workplace safer for everyone. This proactive approach is vital for minimizing costs related to equipment repair and downtime, thus supporting a more productive and safe work environment.
What is Equipment Damage Report?
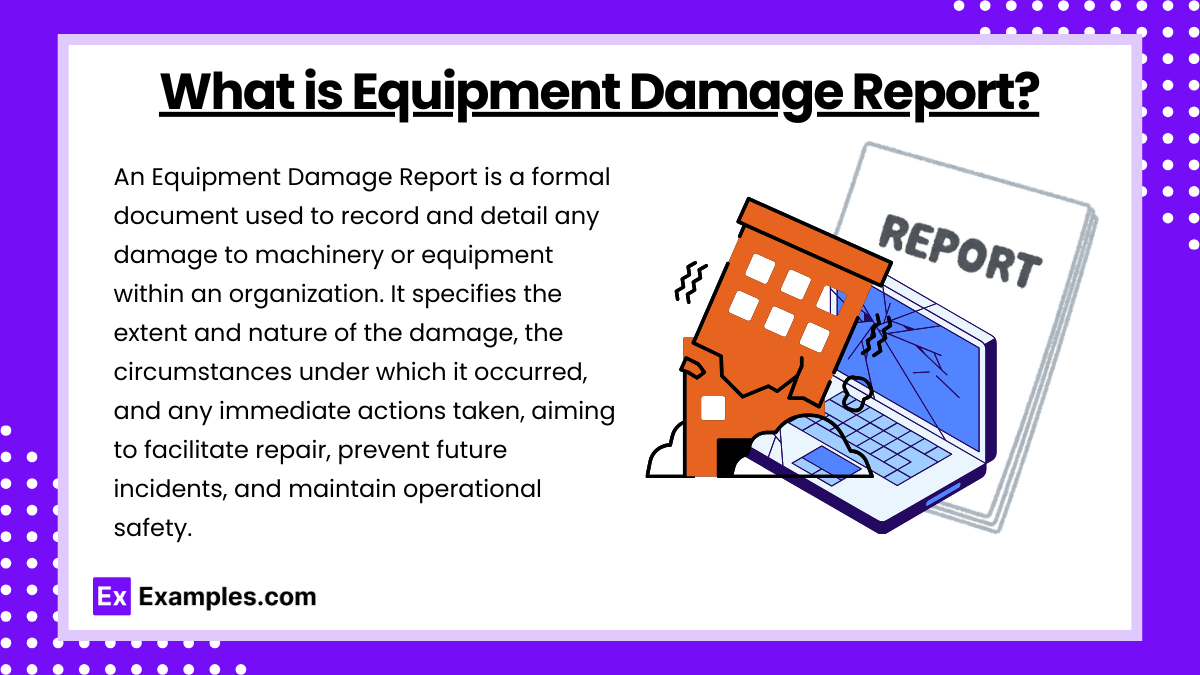
Equipment Damage Report Format
Report Details
Report ID
Date and Time of Report
Prepared by (Name and Position)
Location of Incident
Equipment Details
Equipment Name/ID
Manufacturer
Model/Serial Number
Description of Equipment
Incident Description
Date and Time of Incident
Description of what occurred
Immediate actions taken
Damage Assessment
Type and Extent of Damage
Photos of Damage (if applicable)
Estimated Cost of Repair
Witness Statements
Name and Contact Information of Witnesses
Witness Accounts
Preliminary Cause of Damage
Possible Immediate Causes
Contributing Factors
Corrective Actions and Recommendations
Immediate Corrective Actions Taken
Recommendations to Prevent Future Occurrences
Job Safety Analysis
Hazards Identified Related to the Damage
Safety Measures Proposed
Approval and Follow-up
Signature of Supervisor/Manager
Date of Review
Scheduled Follow-up Actions
Equipment Damage Report Sample
Report Details
- Report ID: 10234
- Date and Time of Report: January 3, 2025, 10:00 AM
- Prepared by: John Doe, Maintenance Supervisor
- Location of Incident: Workshop Area C
Equipment Details
- Equipment Name/ID: Conveyor Belt 5
- Manufacturer: ConveyTech Industries
- Model/Serial Number: CT-5000 / SN-CT50003421
- Description of Equipment: A heavy-duty conveyor belt used for transporting materials across the plant.
Incident Description
- Date and Time of Incident: January 2, 2025, 3:45 PM
- Description of What Occurred: The conveyor belt suddenly stopped working, emitting a loud grinding noise followed by smoke from the motor area.
- Immediate Actions Taken: The equipment was immediately shut down, and the area was secured to prevent personnel access.
Damage Assessment
- Type and Extent of Damage: Severe damage to the motor and the belt alignment system.
- Photos of Damage: [Attached as separate files]
- Estimated Cost of Repair: Approximately $4,500
Witness Statements
- Name and Contact Information of Witnesses:
- Alice Smith, Operator (alice.smith@email.com)
- Bob Johnson, Technician (bob.johnson@email.com)
- Witness Accounts: Both witnesses reported hearing unusual sounds from the motor before it stopped working and observed smoke emanating from it.
Preliminary Cause of Damage
- Possible Immediate Causes: Failure of motor bearings due to lack of regular maintenance.
- Contributing Factors: Inadequate lubrication and overload of the conveyor system.
Corrective Actions and Recommendations
- Immediate Corrective Actions Taken: Replacement of damaged motor and realignment of the conveyor belt.
- Recommendations to Prevent Future Occurrences: Implement a more rigorous maintenance schedule for the conveyor systems and train staff on early detection of equipment malfunctions.
Job Safety Analysis
- Hazards Identified Related to the Damage: Risk of fire from overheating motors and potential injury from sudden equipment stoppage.
- Safety Measures Proposed: Regular inspection of motor conditions and immediate replacement of components showing signs of wear.
Approval and Follow-up
- Signature of Supervisor/Manager: [John Doe]
- Date of Review: January 4, 2025
- Scheduled Follow-up Actions: Follow-up inspection scheduled for January 15, 2025, to ensure all corrective measures have been properly implemented.
Equipment Damage Report Examples
Equipment Damage Report Template
Editable Equipment Damage Report Template
Property Damage Report Template
Equipment Damage Report Form
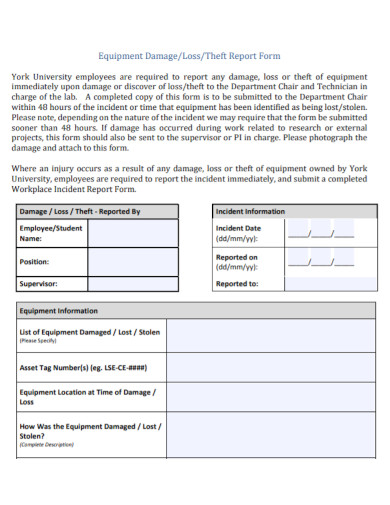
Property Equipment Damage Report
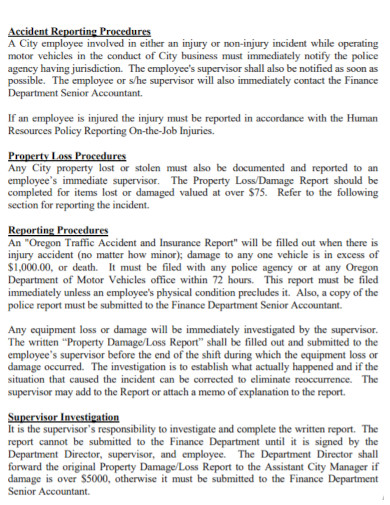
Equipment Damage Report Template
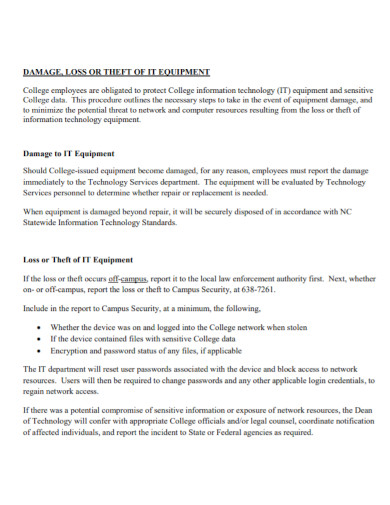
Employees Equipment Damage Report
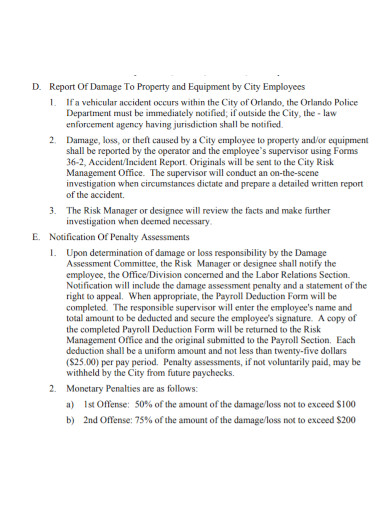
How to Write Equipment Damage Report
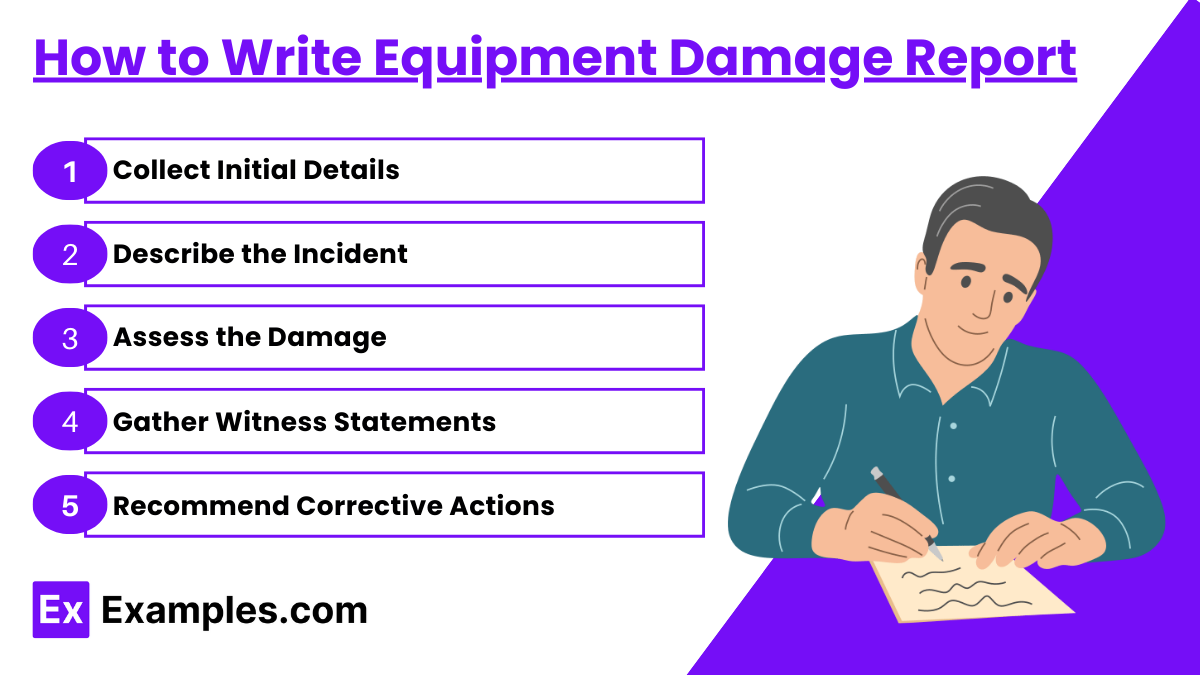
- Collect Initial Details: Begin by gathering all the initial information such as the date, time, and location of the incident, the equipment involved, and the person who is preparing the report.
- Describe the Incident: Provide a clear and concise description of what occurred, including any events leading up to the damage. Document the sequence of events to establish a timeline.
- Assess the Damage: Examine and record the extent of the damage. Include visual evidence such as photographs and describe the type of damage. Estimate the cost for repairs and document any immediate actions taken to mitigate further loss.
- Gather Witness Statements: If applicable, collect accounts from witnesses who observed the incident. Record their names, contact information, and detailed statements regarding what they saw and heard.
- Recommend Corrective Actions: Propose measures to prevent future occurrences based on the analysis of the incident. Include safety recommendations and any changes to procedures that could help avoid similar incidents in the future. Also, outline the follow-up actions planned or already in progress to address the damage and prevent recurrence.
FAQs
Why is an Equipment Damage Report necessary?
It helps manage repairs, improve safety, and prevent future equipment failures through systematic documentation.
Who should complete an Equipment Damage Report?
Typically, the person responsible for the equipment or a designated safety officer completes the report.
What should be included in an Equipment Damage Report?
Incident details, damage assessment, witness statements, corrective actions, and follow-up measures.
How soon should an Equipment Damage Report be filed after an incident?
It should be completed as soon as possible to ensure accurate and useful documentation.
What is the role of Job Safety Analysis in an Equipment Damage Report?
It identifies potential hazards and proposes safety measures to prevent future incidents related to the equipment damage.
6+ Equipment Damage Report Examples to Download
An Equipment Damage Report is an essential document used to record any damage that occurs to machinery or equipment within a workplace. The purpose of creating such a report is to track the specifics of what happened, determine how it happened, and suggest measures to prevent future occurrences. This report is crucial not only for maintaining the equipment but also for ensuring operational safety and efficiency. Incorporating elements of a Job Safety Analysis, it helps identify potential hazards that could harm workers and disrupt daily operations. By analyzing equipment damage in this structured way, companies can improve their maintenance routines and safety protocols, making the workplace safer for everyone. This proactive approach is vital for minimizing costs related to equipment repair and downtime, thus supporting a more productive and safe work environment.
What is Equipment Damage Report?
An Equipment Damage Report is a formal document used to record and detail any damage to machinery or equipment within an organization. It specifies the extent and nature of the damage, the circumstances under which it occurred, and any immediate actions taken, aiming to facilitate repair, prevent future incidents, and maintain operational safety.
Equipment Damage Report Format
Report Details
Report ID
Date and Time of Report
Prepared by (Name and Position)
Location of Incident
Equipment Details
Equipment Name/ID
Manufacturer
Model/Serial Number
Description of Equipment
Incident Description
Date and Time of Incident
Description of what occurred
Immediate actions taken
Damage Assessment
Type and Extent of Damage
Photos of Damage (if applicable)
Estimated Cost of Repair
Witness Statements
Name and Contact Information of Witnesses
Witness Accounts
Preliminary Cause of Damage
Possible Immediate Causes
Contributing Factors
Corrective Actions and Recommendations
Immediate Corrective Actions Taken
Recommendations to Prevent Future Occurrences
Job Safety Analysis
Hazards Identified Related to the Damage
Safety Measures Proposed
Approval and Follow-up
Signature of Supervisor/Manager
Date of Review
Scheduled Follow-up Actions
Equipment Damage Report Sample
Report Details
Report ID: 10234
Date and Time of Report: January 3, 2025, 10:00 AM
Prepared by: John Doe, Maintenance Supervisor
Location of Incident: Workshop Area C
Equipment Details
Equipment Name/ID: Conveyor Belt 5
Manufacturer: ConveyTech Industries
Model/Serial Number: CT-5000 / SN-CT50003421
Description of Equipment: A heavy-duty conveyor belt used for transporting materials across the plant.
Incident Description
Date and Time of Incident: January 2, 2025, 3:45 PM
Description of What Occurred: The conveyor belt suddenly stopped working, emitting a loud grinding noise followed by smoke from the motor area.
Immediate Actions Taken: The equipment was immediately shut down, and the area was secured to prevent personnel access.
Damage Assessment
Type and Extent of Damage: Severe damage to the motor and the belt alignment system.
Photos of Damage: [Attached as separate files]
Estimated Cost of Repair: Approximately $4,500
Witness Statements
Name and Contact Information of Witnesses:
Alice Smith, Operator (alice.smith@email.com)
Bob Johnson, Technician (bob.johnson@email.com)
Witness Accounts: Both witnesses reported hearing unusual sounds from the motor before it stopped working and observed smoke emanating from it.
Preliminary Cause of Damage
Possible Immediate Causes: Failure of motor bearings due to lack of regular maintenance.
Contributing Factors: Inadequate lubrication and overload of the conveyor system.
Corrective Actions and Recommendations
Immediate Corrective Actions Taken: Replacement of damaged motor and realignment of the conveyor belt.
Recommendations to Prevent Future Occurrences: Implement a more rigorous maintenance schedule for the conveyor systems and train staff on early detection of equipment malfunctions.
Job Safety Analysis
Hazards Identified Related to the Damage: Risk of fire from overheating motors and potential injury from sudden equipment stoppage.
Safety Measures Proposed: Regular inspection of motor conditions and immediate replacement of components showing signs of wear.
Approval and Follow-up
Signature of Supervisor/Manager: [John Doe]
Date of Review: January 4, 2025
Scheduled Follow-up Actions: Follow-up inspection scheduled for January 15, 2025, to ensure all corrective measures have been properly implemented.
Equipment Damage Report Examples
Equipment Damage Report Template
Editable Equipment Damage Report Template
Property Damage Report Template
Equipment Damage Report Form
Property Equipment Damage Report
Equipment Damage Report Template
Employees Equipment Damage Report
How to Write Equipment Damage Report
Collect Initial Details: Begin by gathering all the initial information such as the date, time, and location of the incident, the equipment involved, and the person who is preparing the report.
Describe the Incident: Provide a clear and concise description of what occurred, including any events leading up to the damage. Document the sequence of events to establish a timeline.
Assess the Damage: Examine and record the extent of the damage. Include visual evidence such as photographs and describe the type of damage. Estimate the cost for repairs and document any immediate actions taken to mitigate further loss.
Gather Witness Statements: If applicable, collect accounts from witnesses who observed the incident. Record their names, contact information, and detailed statements regarding what they saw and heard.
Recommend Corrective Actions: Propose measures to prevent future occurrences based on the analysis of the incident. Include safety recommendations and any changes to procedures that could help avoid similar incidents in the future. Also, outline the follow-up actions planned or already in progress to address the damage and prevent recurrence.
FAQs
Why is an Equipment Damage Report necessary?
It helps manage repairs, improve safety, and prevent future equipment failures through systematic documentation.
Who should complete an Equipment Damage Report?
Typically, the person responsible for the equipment or a designated safety officer completes the report.
What should be included in an Equipment Damage Report?
Incident details, damage assessment, witness statements, corrective actions, and follow-up measures.
How soon should an Equipment Damage Report be filed after an incident?
It should be completed as soon as possible to ensure accurate and useful documentation.
What is the role of Job Safety Analysis in an Equipment Damage Report?
It identifies potential hazards and proposes safety measures to prevent future incidents related to the equipment damage.